Introduction:
Power cables for machinery are an integral part of any industrial setting. They serve as the lifeline that connects machinery to the power supply, enabling smooth operations and ensuring productivity. However, selecting the right power cable for machinery is crucial to ensure safety, efficiency, and longevity. In this comprehensive guide, we will explore the various types of power cables, their applications, and factors to consider when choosing the most suitable option for your machinery.
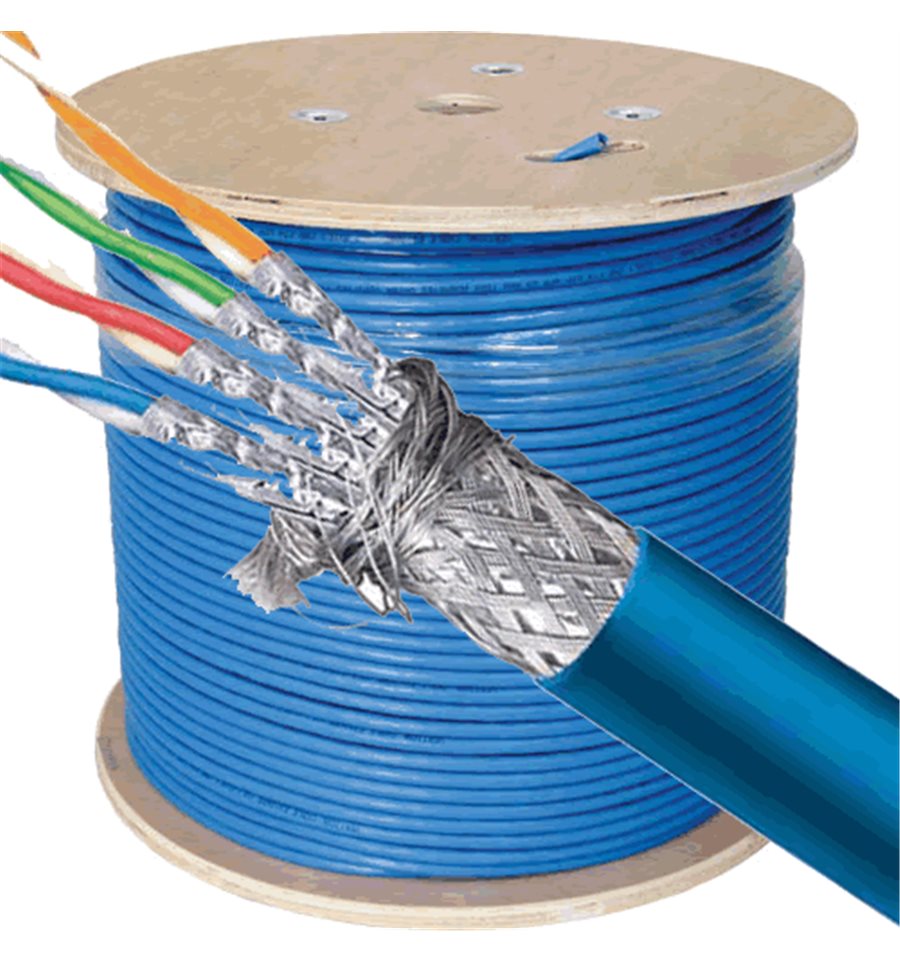
Table of Contents:
1. Understanding Power Cables for Machinery
2. Types of Power Cables for Machinery
a. PVC Power Cables
b. Rubber Power Cables
c. Silicone Power Cables
d. Power cable for generators . Thermoplastic Power Cables
3. Selecting the Right Power Cable for Machinery
a. Voltage and Current Ratings
b. Environmental Considerations
c. Flexibility and Durability
d. Electrical Interference and Shielding
e. Compliance with Safety Standards
4. Installation and Maintenance of Power Cables for Machinery
a. Proper Cable Routing
b. Cable Protection Measures
c. Routine Inspections and Maintenance
d. Replacement and Upgrading
5. Conclusion
1. Understanding Power Cables for Machinery:
Power cables for machinery are specialized cables designed to transmit electrical power from a power source to industrial machinery and equipment. These cables are engineered to withstand the rigors of industrial environments, ensuring reliable power transmission while prioritizing safety and longevity.
In addition to transmitting power, these cables may also include additional conductors for control signals, enabling seamless communication between the machinery and other components in the system.
2. Types of Power Cables for Machinery:
a. PVC Power Cables:
PVC (Polyvinyl Chloride) power cables are versatile and widely used due to their cost-effectiveness and electrical insulation properties. These cables are resistant to moisture, chemicals, and abrasion, making them suitable for various indoor industrial applications. However, they may not be suitable for extreme temperature conditions.
b. Rubber Power Cables:
Rubber power cables are highly flexible and durable, making them ideal for applications that require frequent movement or bending. These cables are resistant to oil, water, and chemicals, making them suitable for outdoor and harsh industrial environments. They also have excellent resistance to temperature variations.
c. Silicone Power Cables:
Silicone power cables are known for their exceptional flexibility, high-temperature resistance, and resistance to UV radiation. They are widely used in industries where exposure to extreme temperatures or outdoor conditions is common. Silicone cables are also resistant to chemicals and have excellent electrical insulation properties.
d. Neoprene Power Cables:
Neoprene power cables are commonly used in heavy-duty industrial applications. They are resistant to oil, solvents, chemicals, and abrasion, making them suitable for demanding environments. Neoprene cables also exhibit good resistance to high temperatures and mechanical stress.
e. Thermoplastic Power Cables:
Thermoplastic power cables are a popular choice for machinery that requires flexibility, durability, and resistance to environmental factors. These cables offer good resistance to moisture, chemicals, and UV radiation. They are also cost-effective and widely available.
3. Selecting the Right Power Cable for Machinery:
a. Voltage and Current Ratings:
The voltage and current ratings of the power cable should match the requirements of the machinery it will be connected to. It is crucial to consider the maximum voltage and current that the cable will encounter during operation to ensure safe and efficient power transmission.
b. Environmental Considerations:
The operating environment of the machinery plays a vital role in selecting the appropriate power cable. Factors such as temperature extremes, exposure to moisture, chemicals, oil, and UV radiation should be considered. Choosing a cable with suitable protection against these environmental factors will ensure longevity and reliable performance.
c. Flexibility and Durability:
The flexibility and durability of the power cable are crucial, especially for machinery that requires frequent movement or bending. Cables with high flexibility and resistance to mechanical stress will minimize the risk of damage and ensure smooth operations.
d. Electrical Interference and Shielding:
In industrial settings, electrical interference can adversely affect the performance of machinery. Shielded power cables, equipped with an additional layer of conductive material, can help minimize electromagnetic interference and ensure reliable power transmission.
e. Compliance with Safety Standards:
Power cables for machinery should comply with relevant safety standards to ensure the safety of personnel and equipment. Compliance with standards such as UL (Underwriters Laboratories) and IEC (International Electrotechnical Commission) ensures that the cable meets the required safety and performance criteria.
4. Installation and Maintenance of Power Cables for Machinery:
a. Proper Cable Routing:
During installation, it is essential to route power cables properly to minimize the risk of damage, interference, or accidental tripping. Cables should be placed away from moving parts, sharp edges, or areas with high foot traffic. Securing https://www.jiangyuancables.com/xlpe-insulated-sheathed-power-cable/ with appropriate clamps or cable trays will prevent unnecessary strain and ensure longevity.
b. Cable Protection Measures:
Power cables in industrial settings are exposed to various hazards, including abrasion, impact, chemical exposure, and moisture. Implementing cable protection measures such as cable conduits, cable carriers, or cable ramps will safeguard the cables and prevent potential damage.
c. Routine Inspections and Maintenance:
Regular inspections of power cables are essential to identify any signs of wear, damage, or degradation. Visual inspections, along with electrical testing, should be conducted periodically to ensure the cables are in optimal condition. Any damaged cables should be promptly replaced to prevent accidents and equipment failure.
d. Replacement and Upgrading:
As technology advances, machinery may require higher power consumption or have different operating conditions. In such cases, it is crucial to assess the existing power cables and determine if they meet the new requirements. Upgrading to cables with higher voltage and current ratings or improved protection features may be necessary to ensure safe and efficient operations.
5. Conclusion:
Power cables for machinery are critical components that provide the necessary electrical connection between industrial machinery and the power supply. Selecting the right power cable, considering factors such as voltage and current ratings, environmental conditions, flexibility, and compliance with safety standards, is crucial to ensure safe and efficient operations.
Proper installation, routine maintenance, and implementing cable protection measures will enhance the longevity of power cables and minimize the risk of accidents and equipment failure. By prioritizing safety, efficiency, and adherence to industry standards, businesses can maximize the productivity and reliability of their machinery.